
Technology
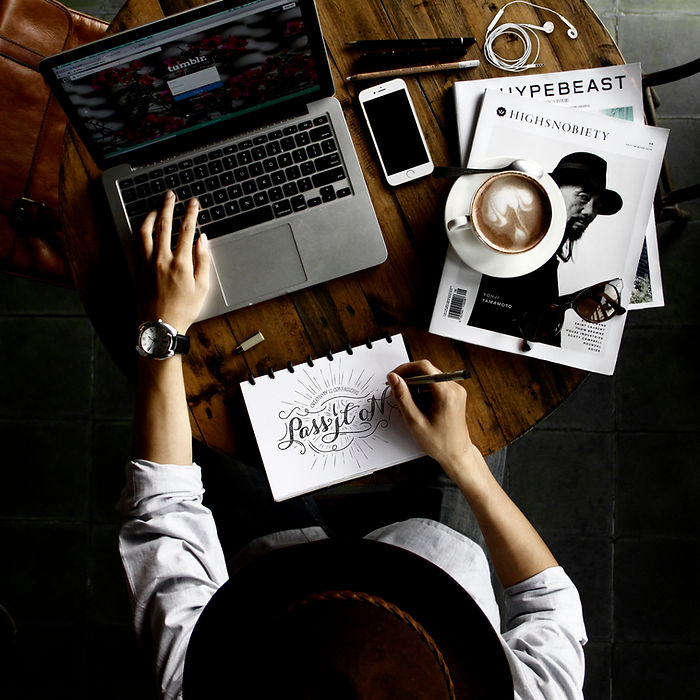


Technology - From powder synthesis
Develop your high-performance materials with us, precisely tailored to your application! Together with our technology partner Glatt Ingenieurtechnik GmbH, we offer our customers
a complete solution based on a wide range of technologies for all sub-steps in material synthesis and thus the optimal technology for the task at hand
Know-how, expertise and innovative strength for the development of application-specific high-performance materials as well
a secure source of raw materials through customer-specific contract manufacturing or through technology and process transfer for in-house production.
We offer the right equipment and supporting know-how for your development, from powder synthesis to ready-to-use dispersion or high-performance granulate. We are the ideal partner for the development, manufacture, processing and application of complex particle systems. We would be happy to modify the material systems for you so that they can be easily incorporated into the product matrix.
APPtec® - A new generation of powder materials
APPtec is a continuous, unique thermal process for the production of powders. The heart of the ProAPP is the specially designed combustion chamber. A pulsating stream of hot gas is generated there, in which the particles are formed and treated. The pulsating gas flow results in special thermodynamic conditions which lead to extraordinary properties of the powders produced.
The extraordinary thermodynamic conditions
lead to special properties and enable
exact configuration of the particles with combinations of properties that did not exist before. To set the material properties, the frequency, amplitude, process temperature and flow speed of the hot gas flow can be precisely adjusted.
Pulsating gas flows show due to the high
Degree of turbulence no temperature and velocity gradients, as they are typical for continuous gas flows. This means that all particles undergo the identical temperature / residence time treatment as the basis for homogeneous powder materials.
To produce particles, a raw material solution is sprayed into the pulsating gas flow in fine droplets. Out
particles form in these drops. These are heated up
where chemical and mineralogical reactions take place.
The particles are then cooled down.
The use of APPtec is particularly efficient because different process steps can be combined into one step, e.g. B. drying and calcination or particle formation and coating together. See for yourself!

Innovative fluidized bed and spouted bed technology
In processes with innovative fluidized bed and spouted bed technologies from our technology partner Glatt
you have almost unlimited possibilities for the best
Particle design and suitable functionalizations of
Granules available. Regardless of whether the product moves quickly,
slowly or not at all should resolve whether instant properties
or maximum particle resistance is required - with the
Technology platform from Glatt and our application
Know-how we offer you the solution.
Glatt has a uniquely broad portfolio
various system concepts for the implementation of
Product ideas with very different requirements.
Batch or continuous operation, single or multi-stage process
Systems, vertical or horizontal material flow - these
many options allow for process development and
Plant engineering together with you, open-ended
to be able to proceed. Each system series was designed for
developed and thus enables certain areas of application
the realization of your product developments.
A fluidized bed is created when flowing upwards
Process air lifts a layer of solid particles - them
fluidized. The process air is used to generate the
Fluidized bed state. At the same time she performs the required
thermal energy for the particle engineering processes.
The spouted bed technology is also based on the
Basic principle of the fluidization of particles through upwards
flowing process air. The main difference is that
patented design of the process air inlet as
Stomata in connection with special flow profiles
as well as a greatly expanding process space. From it
result in significantly higher heat and
Mass transfer rates for processing sensitive
Products with short dwell times.
Benefit from optimal manufacturing processes
high-quality granulates and pellets, also on request
structured and functionalized customer-specific.
